
G40 Galvanized Coil
Category:
Galvanized Steel Coil
Chat with us now for a quick response.
Get expert sales advice within 12 hours.
Keyword:
G40 Galvanized Coil
PRODUCT DETAILS
G40 Galvanized Coil Description
The coating designation G40 represents the type of coating and the weight of the applied coating. The letter "G" indicates that the coating is galvanized, meaning zinc-based. Meanwhile, the number "40" represents the weight of zinc on the surface of the steel sheet.
Galvanized steel coils are covered with a zinc coating to provide corrosion resistance. G40 galvanized steel coil is a galvanized layer name or A653 standard specification specified in the hot-dip coating process galvanized (galvanized) or zinc-iron alloy (galvanized) steel sheet requirements. The G40 protective coating prevents moisture from reaching the steel structure, thereby improving the corrosion resistance of the steel. This can extend the life expectancy of the steel. G40 is the average coat weight and therefore provides moderate protection.
Scope of Application
Galvanizing products are widely used in industry, agriculture, animal husbandry and fishery, energy, transportation, chemical industry, light industry, home appliances, construction, communications, national defense and other fields.
Product Parameters
Product Name |
G40 Galvanized Coil |
Thickness |
0.12mm-3.5mm |
Width |
600mm-1500mm |
Length |
508mm/610mm, Support Customization |
Standard |
AISI, ASTM, DIN, JIS, GB, JIS, SUS, EN, etc. |
Zinc Layer |
Hot Galvanizing: 60-275g/m² |
Pre-galvanized: 80-275g/m² |
Chemical Composition
Standard |
Grade |
C |
Si |
Mn |
P |
S |
Ti |
Forcold Forming Chinese Standard |
DX51D+Z |
0.12 |
0.50 |
0.60 |
0.100 |
0.045 |
0.30 |
DX52D+Z |
0.12 |
0.50 |
0.60 |
0.100 |
0.045 |
0.30 |
|
DX53D+Z |
0.12 |
0.50 |
0.60 |
0.100 |
0.045 |
0.30 |
|
DX54D+Z |
0.12 |
0.50 |
0.60 |
0.100 |
0.045 |
0.30 |
|
DX56D+Z |
0.12 |
0.50 |
0.60 |
0.100 |
0.045 |
0.30 |
|
DX57D+Z |
0.12 |
0.50 |
0.60 |
0.100 |
0.045 |
0.30 |
|
Forcold Forming Japanese Standard |
SGCC |
0.15 |
0.50 |
0.80 |
0.050 |
0.030 |
0.025 |
SGCD1 |
0.12 |
0.50 |
0.60 |
0.040 |
0.030 |
0.025 |
|
SGCD3 |
0.08 |
0.50 |
0.45 |
0.030 |
0.030 |
0.025 |
|
SGCD4 |
0.06 |
0.50 |
0.45 |
0.030 |
0.030 |
0.025 |
|
For Structure Japanese Standard |
SGC340 |
0.25 |
0.50 |
1.70 |
0.200 |
0.035 |
0.025 |
SGC400 |
0.25 |
0.50 |
1.70 |
0.200 |
0.035 |
0.150 |
|
SGC490 |
0.30 |
0.50 |
2.00 |
0.200 |
0.035 |
0.025 |
|
SGC510 |
0.30 |
0.50 |
2.50 |
0.200 |
0.035 |
0.025 |
|
For Structure AISI Standard |
S220GD+Z |
0.20 |
0.60 |
0.70 |
0.100 |
0.045 |
0.025 |
S250GD+Z |
0.20 |
0.60 |
0.70 |
0.100 |
0.045 |
0.025 |
|
S280GD+Z |
0.20 |
0.60 |
0.70 |
0.100 |
0.045 |
0.025 |
|
S320GD+Z |
0.20 |
0.60 |
0.70 |
0.100 |
0.045 |
0.025 |
|
S350GD+Z |
0.20 |
0.60 |
0.70 |
0.100 |
0.045 |
0.150 |
|
S550GD+Z |
0.20 |
0.60 |
0.70 |
0.100 |
0.045 |
0.150 |
Mechanical Properties
Grade |
Yield Strength MPa≥ |
Tensile Strength MPa≥ |
Elongation A%≥ |
DX51D Z/ZM/AZ/AM |
240-380 |
270-500 |
22 |
DX52D Z/ZM/AZ/AM |
140-300 |
270-420 |
26 |
DX53D Z/ZM/AZ/AM |
140-260 |
270-380 |
30 |
DX54D Z/ZM/AZ/AM |
120-220 |
260-350 |
36 |
S220GD Z/ZM/AM |
220 |
300 |
20 |
S250GD Z/ZM/AZ/AM |
250 |
330 |
19 |
S280GD Z/ZM/AM |
280 |
360 |
18 |
S300GD A/AM |
300 |
380 |
18 |
S320GD Z/ZM/AM |
320 |
390 |
17 |
S350GD Z/ZM/AZ/AM |
350 |
420 |
16 |
S450GD A/AM |
450 |
480 |
15 |
S550GD Z/ZM/AZ/AM |
550 |
550 |
- |
Galvanized Surface Selection
Zero Spangle |
Minimized Spangle |
Normal Spangle |
Large Spangle |
|
|
|
|
Use of The Environment |
Recommended Zinc Thickness |
Indoor Use |
Z10 or Z12 (100g/㎡or 120g/㎡) |
Suburbs |
Z20 and Painting (200g/㎡) |
Urban or Industrial Area |
Z27 (270g/㎡) or G90 (US Standard) and painted |
Coastal Area |
Thicker than Z27 (270g/㎡) or G90 (US Standard) and painted |
Punch or Deep Drawing Application |
Thicker than Z27 (270grams/㎡) or G90 (US Standard) avoid coating peeling after stamping |
Surface Treatment Type |
Code |
Features |
Chromic Acid Treatment |
C |
Good corrosion resistance, suitable for bare state |
Chromic Acid Treatment+Oiling |
S |
Good corrosion resistance |
Phosphoric Acid Treatment (Including Sealing Treatment) |
P |
Have a certain corrosion resistance, good paint performance |
Phosphoric Acid Treatment (Including Sealing Treatment)+Oiling |
Q |
Has a certain corrosion resistance, good paint performance, prevent rust during transportation and storage |
Phosphoric Acid Treatment (Excluding Sealing Treatment) |
T |
Have a certain corrosion resistance, good paint performance |
Phosphoric Acid Treatment (Excluding Sealing Treatment)+Oiling |
V |
Has a certain corrosion resistance, good paint performance, and prevent rust |
Oiling |
O |
Prevent rust during transportation and storage |
No Treatment |
M |
Suitable for immediate painting |
Material Comparison
Chinese Standard |
Japan Standard |
European Standard |
DX51D Z/DC51D Z (CR) |
SGCC |
DX51D Z |
DX52D Z/DC52D Z |
SGCD1 |
DX52D With |
DX53D Z/DC53D Z/DX54D Z/DC54D Z |
SGCD2/SGCD3 |
DX53D Z/DX54D Z |
S220/250/280/320/350/550GD Z |
SGC340/400/440/490/570 |
S220/250/280/320/350GD Z |
DX51D Z/DD51D Z (HR) |
SGHC |
DX51D Z |
Packing and delivery
Our annual sales are 8,000 tons. It is the top steel service provider and steel solution provider in the region. The company has a powerful sales team to provide customers with comprehensive technical support, pre -sales service and comprehensive after -sales service. The entire perfect treatment and sales process is our quality assurance.
FACTORY
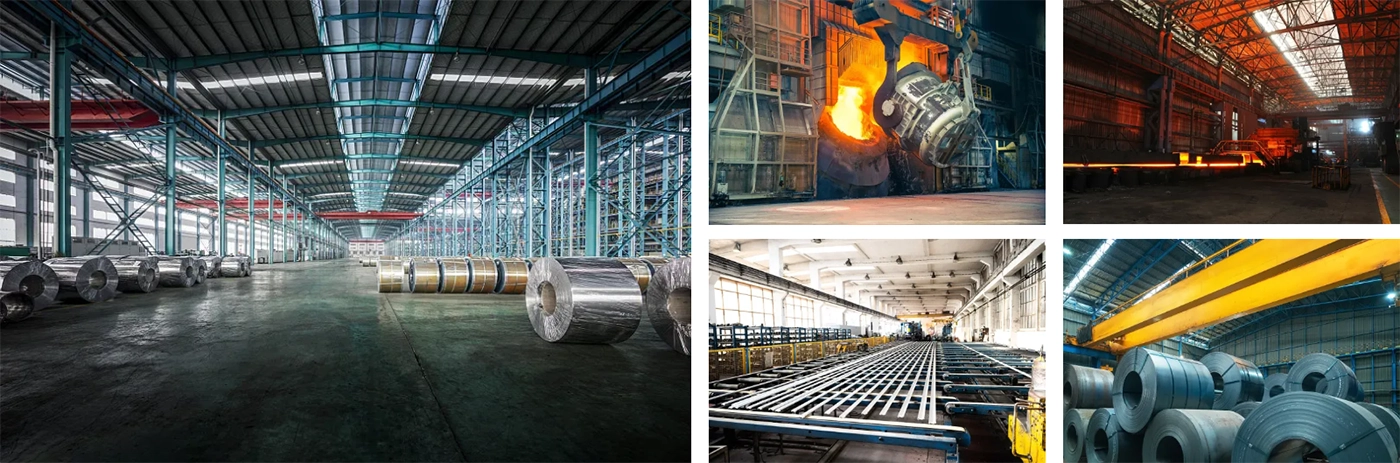
CUSTOMER VISIT
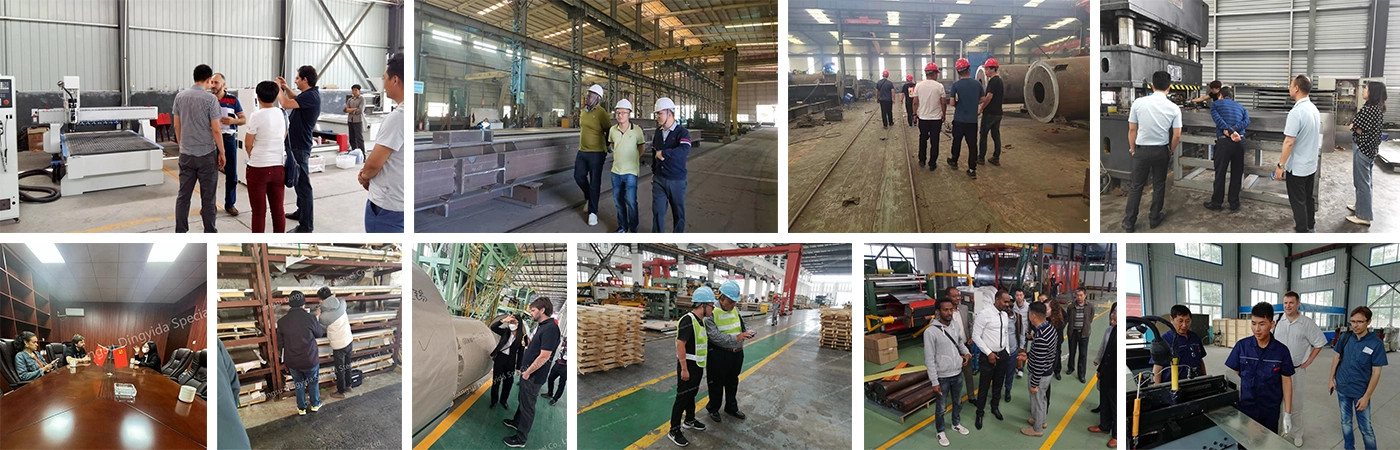
Customer communication

Partner
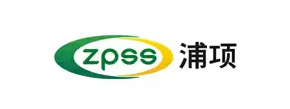
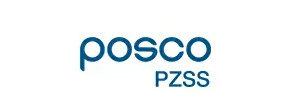

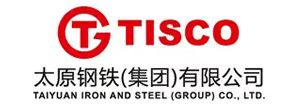
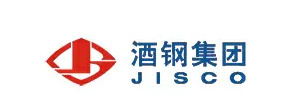
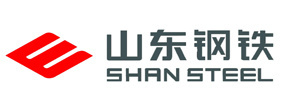
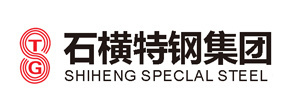
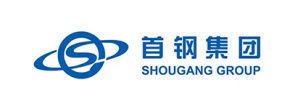
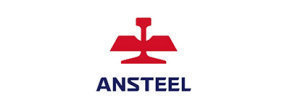


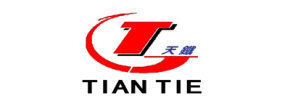
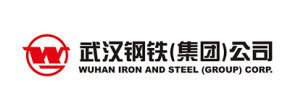
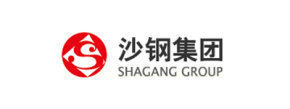
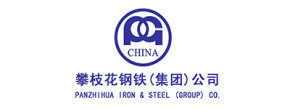
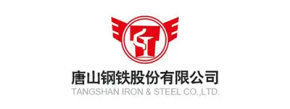
COMMON PROBLEM
OUR HONOR
APPLICATION SCENARIOS
Oil field
Aircraft manufacturing
Train manufacturing
Ship manufacturing
Power industry
Construction industry
GET A FREE QUOTE
RELATED PRODUCTS